The Journey of a Single Flower
Ever wondered how that lush bouquet of Ever Red roses, dreamy Baccarat carnations or tinkerbell-esque calla lilies made it to your hands or adorned the vases in your homes and workspaces? The mind goes to answer it quite simply, of course - from the garden to the florist to my hands by way of my wallet. Indeed, it could be that simple but it isn’t. The journeys of these flowers often span distances across cities, countries and even continents and pass delicately through various pit-stops to finally reach you. We’d like to give you a little glimpse of that journey right here.
Let's start from the ground up (quite literally). Our gorgeous homegrown flowers are sourced from a wide array of farms all over Kenya. Known for its sunny climate and prime freshwater resources, Kenya provides for optimal fertility when it comes to growing high quality, long-lasting roses, carnations, lilies, hydrangeas and much more. The location of farms plays a very important role too. Farms at higher altitudes produce larger blooms which are popular in Eastern European markets where consumers tend to buy 1 or 2 singular stems. As we move closer to the ground, the growing conditions are more compatible for medium sized flowers and these are popular with Western and Northern European countries where flowers are generally bought in bunches. The country has developed their logistical links to Europe to further easen the shipping process for fresh cut flowers while also dedicating an entire terminal at the Nairobi airport to the transportation of fresh flowers and vegetables. We take great pride in working with farms that are highly quality-conscious and embody ethical trade practices and sustainability to the best of their abilities.
While our beauties are being nourished and readied for harvest, our clients (wholesalers and large retailers) place their orders with us. Details of the type and variety of flowers, their expected dates of delivery, etc are all collected in order to provide accurate cost estimates for the order. We expect these orders to be placed a minimum of 4 days in advance in order to organize sourcing, freight and other details with sufficient time in hand.
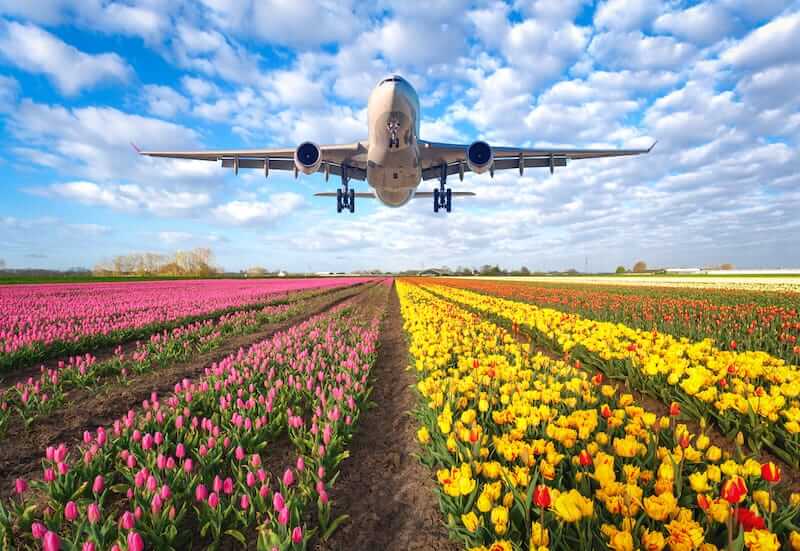
Once an order is placed and confirmed, we swiftly move to book spaces with the airlines and plan the palletising process. This stage usually takes a significant amount of time since we try to make the best use of space while coordinating multiple orders for different customers (different destinations). We also have to take the loading equipment to be used, into account. For example, using PLA allows us to use 72 boxes versus using PMC which accommodates 120 boxes if the upper deck is available or 96 boxes in the case of the lower deck. And this process isn’t limited to planning for the type of boxes but meeting airlines’ requirements as well. For example, some airlines have a pivot weight where you would have to meet a minimum weight on a specific piece of equipment. TK pivot weight is 1650kg on 96 boxes, lower deck – so we are charged for 1650kg even if our final shipments only weigh 1400kg with the same 96 boxes. This means we essentially lose 250kg in ‘dead freight’. The efforts put into the planning process help us reduce waste in our supply chain and ensure optimal utilization of all our resources at any given moment.
We then organize our orders to be circulated within our network of farms so as to have the required flowers in the right quantities available for delivery. The delivery is made on the day of departure to avoid long durations between storage, shipment and final delivery. The flowers make their way from the several farms around Kenya to the airport where they are stored in cold rooms. Due to our high traffic usage with multiple orders going out each week, we have been fortunate enough to procure a cold room solely for our shipments. This is not the case usually and different shipments from different companies are stored together. While this is not usually an issue, it can lead to delays or damage to the flowers arising from mishandling of the cargo. It is important to note that some flowers often require special care while transporting so the process is not one-size-fits-all. Hydrangeas, for example, are much more delicate than roses or carnations and need to be stored at temperatures between 5 and 8 degrees Celsius. Most other flowers require temperatures between 2 and 4 degrees Celsius. This proves to be quite a big difference for a singular cold room that houses all these varieties and types. Furthermore, hydrangeas need to be shipped with a moisture source since they are highly water reliant and tend to dehydrate quickly.
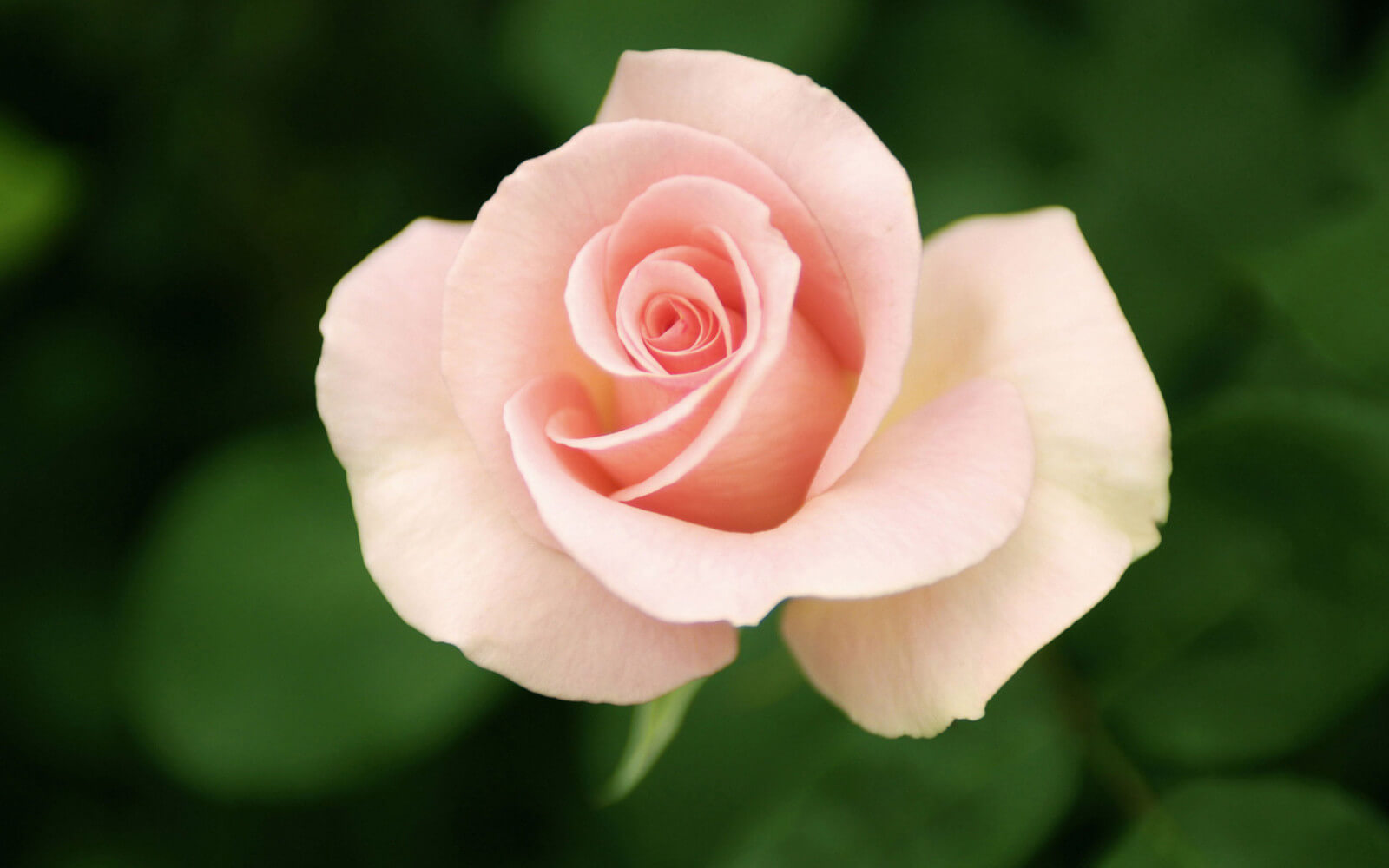
A crucial aspect of this entire process is the quality of our flowers. At Azalea, we pride ourselves on being extremely quality-conscious. We undertake multiple quality checks right from the farms, moving to the airport, in the cold rooms and pre-flight. This translates to several hours spent by our on-ground operations team meticulously going through every box to ensure only the best and freshest blooms are sent to our customers. Any box that doesn’t meet the quality mark is sent back to the farms. There are very few consolidators in the industry who focus on and invest in the quality of shipments as much as us.
One copy of the shipment details is shared with the client for reference and to confirm what they should expect to receive while the other is sent to the on-ground operations team to kick-start the palletising process. Once the shipments are prepared for loading and the appropriate documentation is shared with all necessary personnel (invoices, customs, etc). Shipment details including the varieties, number of stems, etc are then uploaded to the Kenya Plant Health Inspectorate Service (KEPHIS) portal. An inspector from KEPHIS conducts a physical check to ensure that the shipments are free of any health issues such as pests, fungus, etc and provide a Phyto-sanitary Certificate. The clients are updated on the status of the shipment as it departs, connects and lands in the final destination city. We go the extra mile to make sure everything is taken care of until you receive your flowers in hand. All through these stages, Team Azalea is available for assistance and support 24x7. Catering to your needs is our highest priority and we guarantee the best quality not only in flowers but also in our customer relationship management.
As consolidators, this is where we usually bid adieu to our beautiful flower babies. They then travel to other wholesalers or retailers and find their way into your local florists, supermarkets and online stores. This is the journey of one flower from the heart of Kenya into the hearts of your homes and offices.